# Digital Solutions
Zerhusen Kartonagen
Germany
Zerhusen Kartonagen GmbH based in Damme, Germany, has been relying on intelligent solutions from Continental for its tire management since 2014. Starting with the tire-pressure monitoring system ContiPressureCheck™, the company took a step toward intelligent tire monitoring in 2016 as one of the first test customers for ContiConnect™.
With ContiConnect™, the company’s director Roland Zerhusen can keep an eye on every tire in his fleet at all times.
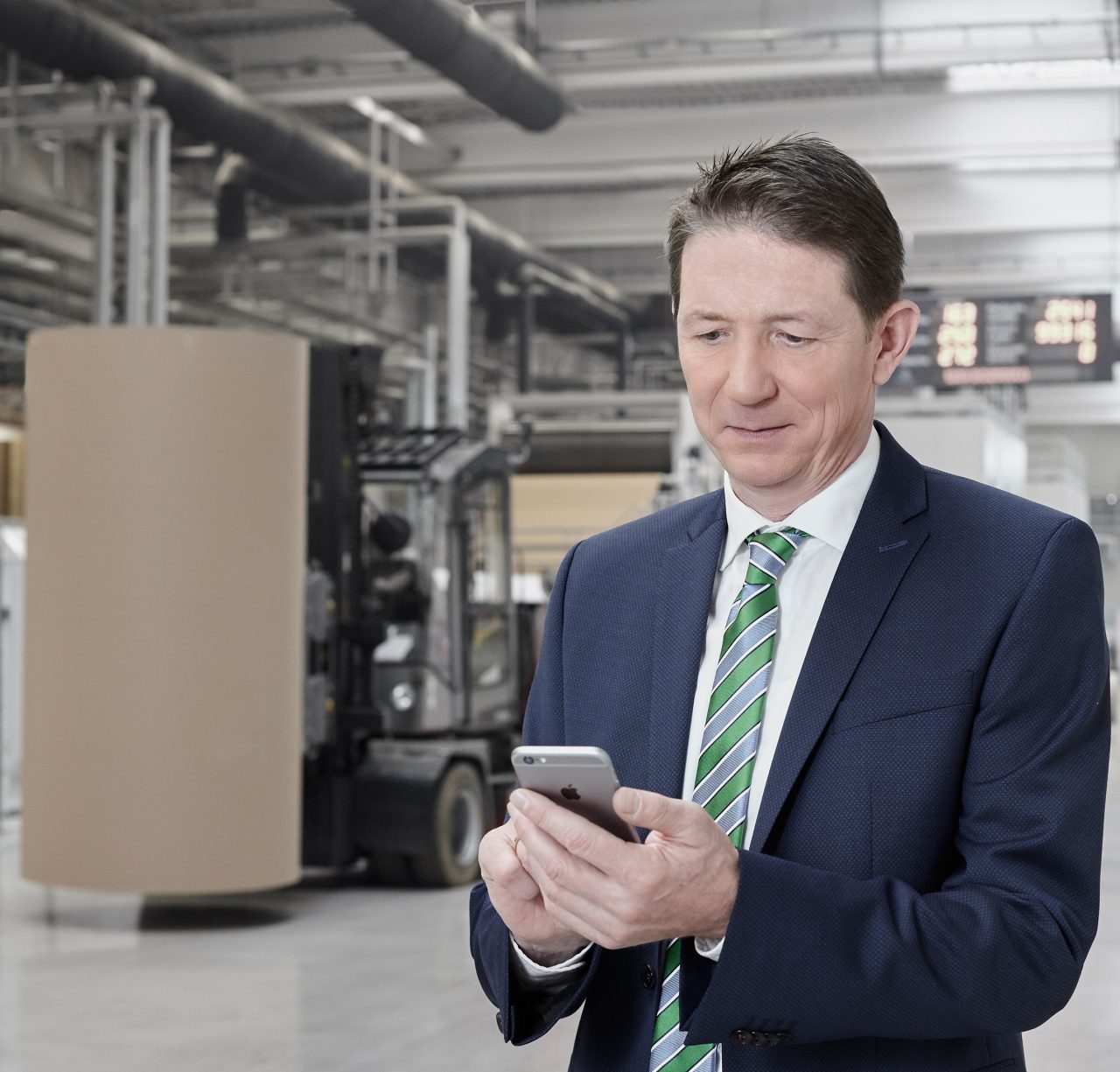
The solution consists of three components: tire sensors that measure tire pressure and temperature inside the tires, a stationary data receiver known as the yard reader, and the web portal. The data is transmitted from the tire sensor to the yard reader, which then sends them to the web portal for analysis via the mobile network. Using the web portal, the vehicle fleet manager can easily monitor the tires’ condition. He also proactively receives an SMS or e-mail if the tire pressure is not right, enabling him to take action accordingly.
Company director Zerhusen can thus focus entirely on his core business, the production and sale of cardboard packaging. In addition to economy and efficiency, his primary focus is on his customers: “Our corrugated cardboard packaging is needed by the food, plastics, and furniture industries for packaging their own products.” The company Zerhusen delivers an average of 70 truckloads of goods each day. “We supply major customers with two or three truckloads a day.” In order to meet the allocated time slots for unloading at the customer, absolutely reliable and punctual delivery is essential.
“Since we started using ContiConnect™, we have so far prevented twelve flat tires,” reports the entrepreneur. “In particular, the intelligent tire management solution has helped us get to grips with the major problem of damage from embedded foreign objects.” In the whole of 2017, the fleet did not suffer a single flat tire as a result of embedded metal components or similar objects.
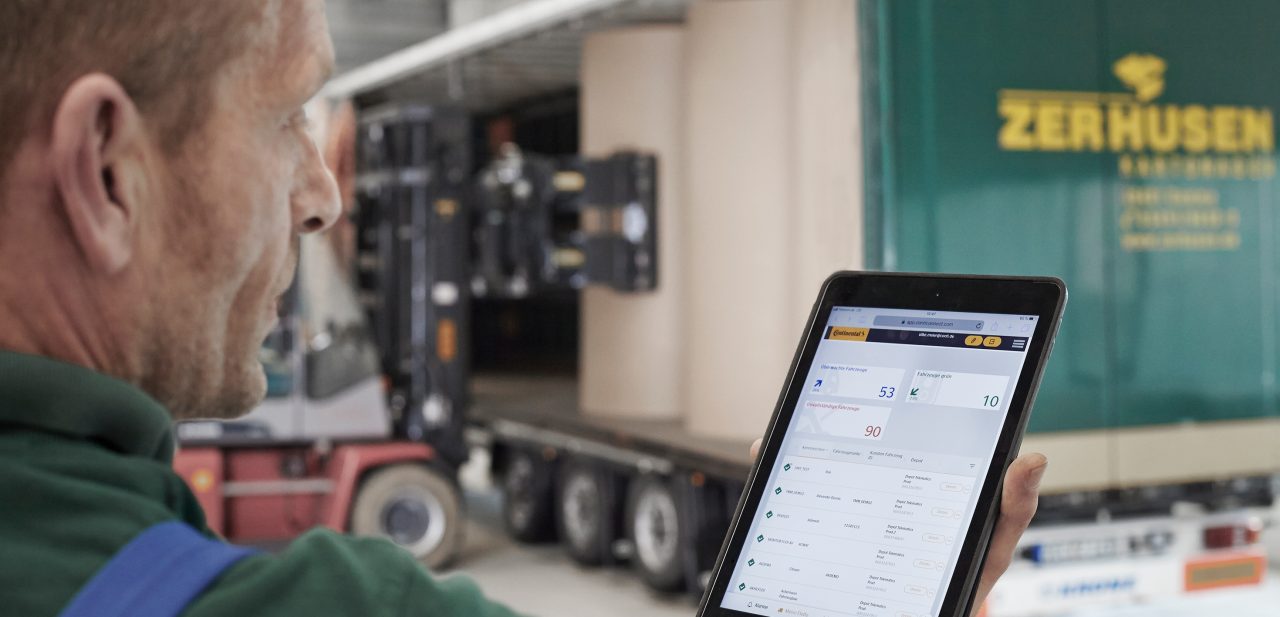
A flat tire doesn't just mess up our schedules annoy our customers, it also results in costs of approximately 1.500€ per tire, which we can now save thanks to ContiConnectTM.
Another benefit is that all vehicles now drive with optimal air pressure at all times. “Before we started using ContiConnect™ in our fleet, we didn’t have any regulated tire-pressure monitoring and didn’t focus on tire pressure,” recalls Zerhusen. Tires were one of the aspects monitored in regular checks in the company’s own auto repair shop. “This solution cannot be replaced with a manual check,” says auto repair shop manager Andreas Knüppe. Continuous monitoring and driving with optimal air pressure now not only helps prevent flat tires and breakdowns, but also saves fuel – an estimated three to four liters per 100 kilometers.
“With the introduction of ContiConnect™ at the latest, the topic of optimal tire pressure is also given high priority by the drivers,” reports Zerhusen. “Not just because it greatly increases driver and vehicle safety, but also because the drivers are no longer left to deal with this issue alone.” All information is provided to the scheduling department and the auto repair shop, meaning that a fast reaction can be ensured. In addition, the company likes to use the topic of ContiConnect™ to enhance its own image. “The drivers talk about it, we tell our customers about it, and we have also covered the topic in our company magazine.” ContiConnect™ has thus quickly become part of the company’s day-to-day business and is accepted and fully integrated.