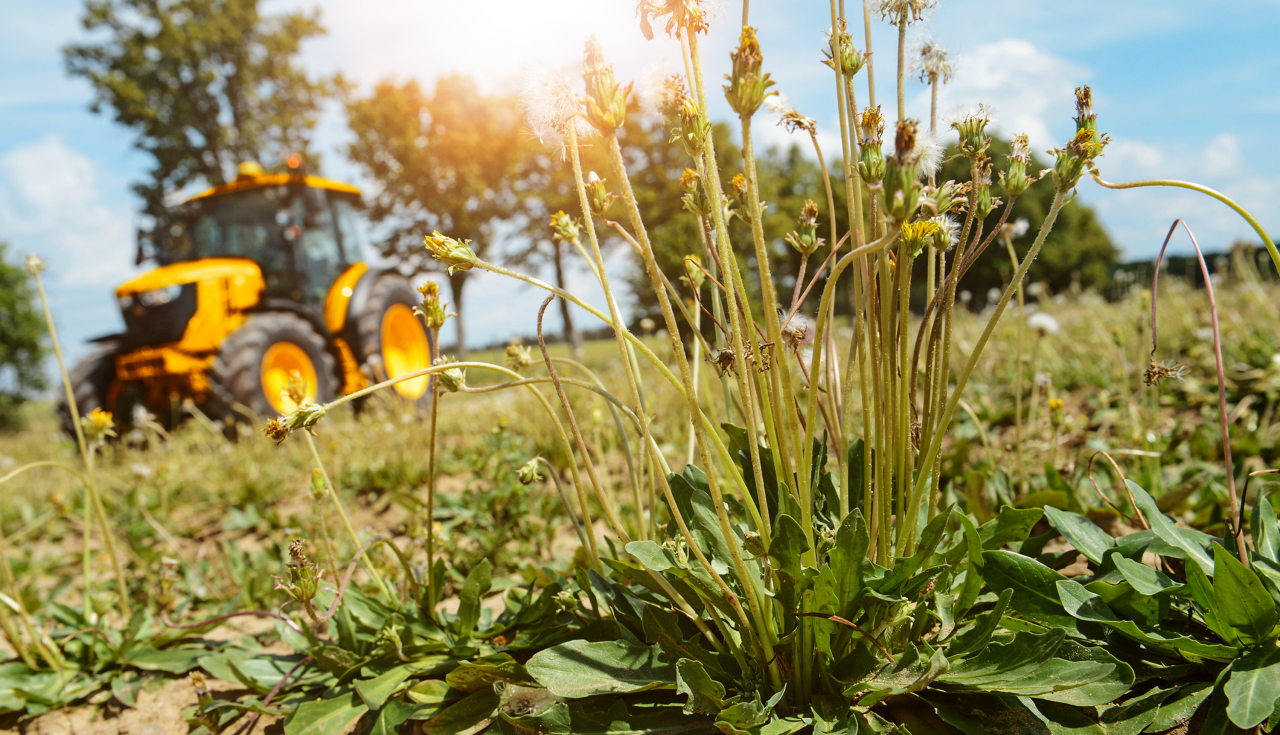
Continental first introduced silica in the tread compounds of car tires 30 years ago, revolutionizing driving safety and energy efficiency. Thanks to the special surface properties of silica, the rolling resistance of tires was significantly reduced and braking distances were almost halved. Today, silica has largely replaced carbon black in the tire tread and has become indispensable for many rubber compounds for car, van and two-wheeled vehicle tires. In addition, the production processes for the filler are becoming increasingly sustainable. Today, Continental already uses sustainable silica obtained from rice husk ashes.
How Continental came to use silica in its tire rubber compounds for the first time and how the company continues to drive this innovation forward today is explained by Continental experts Prof. Burkhard Wies, Head of Applied Research and Innovation, and Dr. Hajo Weinreich, Compound Development Ultra High Performance Tires (UHP).
Wies: Silica is a white, crystalline solid material that occurs naturally in rocks such as flint and quartz. Silica is used as a filler in many industries. In construction, for example, it is used in the production of concrete and bricks. Silica is primarily obtained from quartz sand. However, this crystalline silica is unsuitable for use in tire production, as it does not interact sufficiently with the rubber. Therefore, during a technical process, it is converted into amorphous silica, which is then suitable as a filler for tread rubber compounds. We procure this processed amorphous silica directly from suppliers.
Wies: By using silica (instead of carbon black) as a filler in the tread compound, this massively improves the tire’s wet grip as well as its rolling resistance. At the same time, it can withstand extreme stresses. Together with the introduction of passive safety equipment such as the seat belt, the anti-lock brake system and constructive measures on the passenger vehicle, this "revolution in tire assembly" has helped to significantly reduce the number of road casualties.
Weinreich: Its properties are activated during the mixing process, where it is made to react with a binding agent called silane. Later, during the tire vulcanization process, the rubber compound is pressurized at temperatures of 120°C to 160°C. A tire obtains its characteristic appearance thanks to special tire molds. Sulfur is used to turn the rubber compound into a flexible and elastic rubber. Then, during vulcanization, the sulfur forms the bridge between the long-chain molecular strands of the rubber. The silica – supported by the silane binding agent – forms additional bonds between individual rubber polymers, creating a very strong network between the rubber molecules.
Wies: Back in the 1970s, the first tire manufacturers conducted tests using silica as a solid material in tire compounds. But without success. At the end of 1993, Continental conducted its first tests using silica in tread compounds for car tires. And we succeeded! This made us one of the pioneers to experiment in and conduct lab tests for new tire compounds. In the mid-1990s, we brought the first production tire – the ContiEcoContact CP – onto the market.
Wies: Silica became a success story for rubber compounds. In 1996, the first winter tire – the ContiWinterContact TS 770 – was launched, allowing us to almost halve braking distances on wet road surfaces. This was a major boost to safety, all thanks to the tires – a product that often goes unnoticed. Besides safety, we mustn’t forget the positive impact of the tires on the environment: we were able to reduce rolling resistance by 50%. At the time, this meant less fuel consumption, whereas today, with electric cars, it is primarily about extending the range.
Weinreich: Today, we are looking at development and how we can make the tires even safer and more sustainable while delivering even greater performance. Both when it comes to tire assembly as well as the materials we use. We are researching the use of silica from alternative, more sustainable sources with the equivalent or even improved properties and safety benefits.
The ashes of rice husks have proven to be a reliable base material for sustainably manufactured silica. They are a by-product of rice production that cannot be used as food or animal feed. And manufacturing silica out of rice husk ashes is even more energy-efficient than conventional materials such as quartz sand. It is a win-win. We are already using silica from rice husk ashes in our most sustainable production tire to date – the UltraContact NXT. And this is just the beginning. Our medium-term goal is to procure all our silica from sustainable sources.
Weinreich: No. Premium tires are no longer manufactured without silica compounds. There are still products that rely on carbon black compounds in the tread. But these tires do not perform well in the relevant tests conducted by the trade press – especially when it comes to their safety-related wet properties.
Weinreich: Silica is also used in tires for two-wheeled vehicles. Continental produced the first motorcycle tire using silica in 2002 – the ContiForce. Similar to car tires, the massively improved wet grip is the main argument for using silica compounds in the motorcycle tire segment. Because here we are talking about a tire contact area that is not even the size of two palms of a hand. The story is pretty much the same for bicycle tires, where the wet grip is also extremely important, but the lower rolling resistance compared with a carbon black compound speaks for silica tires. Ultimately, the lower rolling resistance makes the tread lighter. This can also be seen with the hand-made Tour de France tires from Continental.