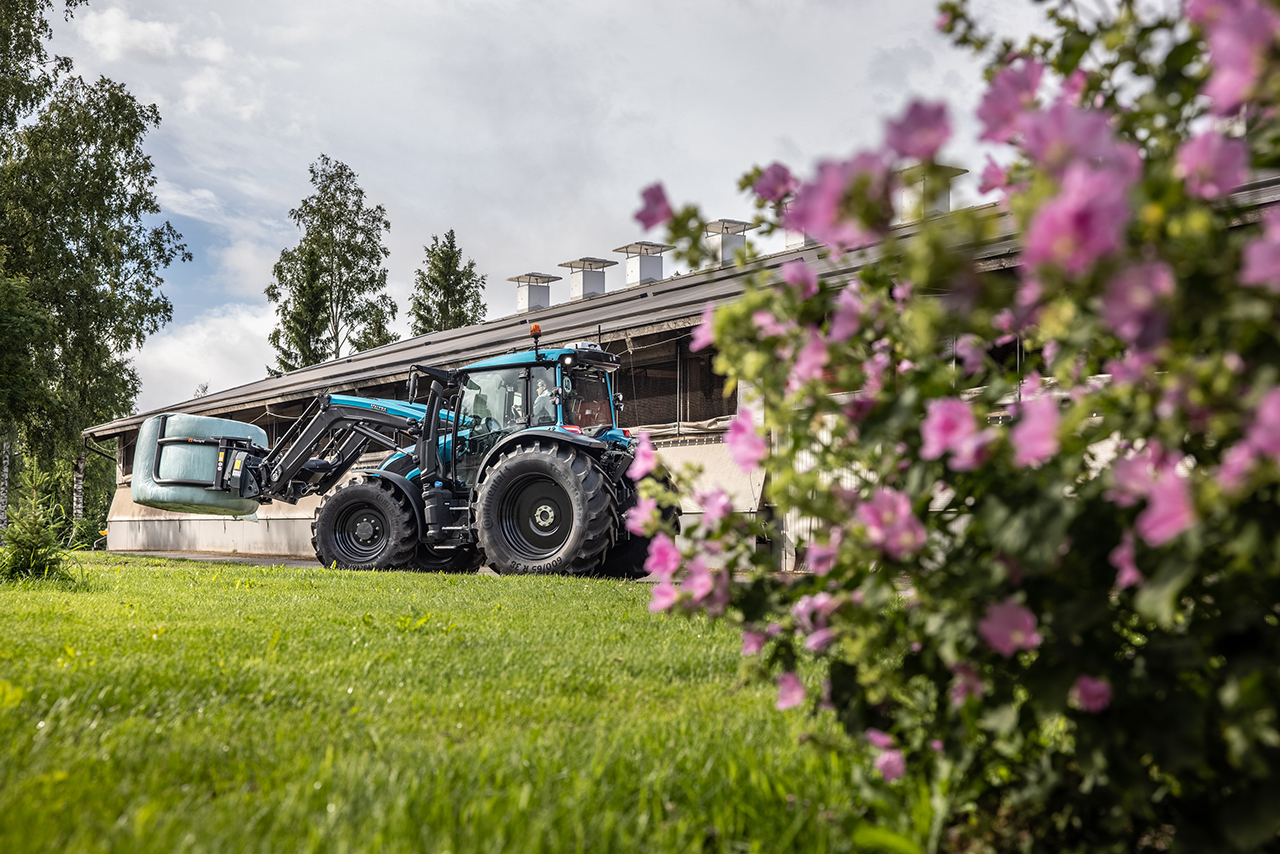
Will robots soon be taking over work in the fields? Will smart machines be replacing tractors, combine harvesters, etc.? And what role will smart tire sensors play in tomorrow's agriculture? Continental spoke with field robotics researcher Professor Arno Ruckelshausen from Osnabrück University of Applied Sciences – just in time for Agritechnica, the world's largest trade fair for agricultural technology.
Prof. Ruckelshausen, Agritechnica was held in Hanover from November 10 to 16. Already in the run-up to the fair there was a lot of talk about Big Data, artificial intelligence, cloud computing and sensor technology in the farming industry. Are farmers soon going to need a degree in computer science to be able to bring in the harvest?
The observation is correct, but the conclusion is not. If we look at the innovations presented at Agritechnica over the past ten years, the degree of innovation has indeed shifted increasingly towards electronics, information technology and sensor systems. Seeding, harvesting and feeding machines are being digitally upgraded. They are networked and becoming increasingly automated. In principle, agricultural technology is playing a pioneering role for other production industries. For example, today, industrial applications are often networked, but then machines in production plants do not usually move around. In agriculture, on the other hand, the machines are mobile, even under difficult outdoor conditions. In the automotive industry, “autonomous driving” is a major trend, but in agriculture, autonomous working is added on. That's in a completely different league. Companies and research centers are developing self-driving work machines that can sow and harvest independently. But does a farmer need a degree in computer science bring in the maize? No, just like a smartphone user doesn't need to be an expert in algorithms to send WhatsApp messages. Because it's all about developing user-friendly systems that offer numerous benefits in the agricultural sector.
So are we witnessing the emergence of agriculture 4.0? A digitally upgraded agricultural sector with smart, networked infrastructure?
Farming 4.0 already exists, and we are even one step ahead of Industry 4.0. In principle, networked, and above all mobile production plants on wheels are being used in agriculture. It's just that a factory like this is called a combine harvester, for example. The challenge is to make complex work processes more economical and ecological through a digital transformation processes. Mobile work processes in the fields run subject to many disturbance variables: rain, storms, snow, uneven, muddy or bone-dry ground. These are huge challenges to the robustness of the technologies used.
As in the automotive industry, there are many new start-ups in the agricultural sector. At Agritechnica, a separate “Agrifuture Lab” where young companies can present digital innovations was build up in Pavilion 11.
“The sector is on the move. Here, in the broader area around Osnabrück, the Silicon Valley of agricultural engineering, we have just founded the “Agrotech-Valley” association with agricultural engineering companies, scientific institutions, business development and start-ups. All those involved have the same goal: to make agriculture ecologically, economically and socially sustainable. You can feel that there's a real sense of a new beginning at the base. Young entrepreneurs and researchers are bringing with them an enormous amount of creativity and dynamism. Computer scientists and experts in artificial intelligence are finding that agriculture is an exciting field for future development challenges.
There's an old cliché of a farmer who hates outsiders telling him how to do his work and prefers to do everything in the same old way. “A farmer won't eat what he's not familiar with,” as they say in Germany. Now computer scientists, or physicists such as yourself, are coming along with robot machines that decide for themselves when the wheat has to be harvested. Aren't two very different worlds clashing there?
Oh, the image of the farmer who hates advice is an old cliché. For example, the Osnabrück University of Applied Sciences works with many agricultural companies, and we come into contact with some very, very open-minded partners. For example, we test autonomous field robots for weed control, autonomous machines for feeding on farms, and innovative sensor technologies for agricultural machinery or plant cultivation. The farmers are supporting the research and the field trials required to design and develop future products.
You are a physicist researching sensor technology. What is the significance of this discipline for agriculture? Where sensors are being used?
In actual fact, everywhere where machines are being made smarter or more efficient for use in an agricultural sector that is increasingly tending towards sustainability. The aim is to use different sensor systems to get an in-depth understanding of every major agricultural issue. In the future, it could mean: no sensors, no harvest. The field is no being longer regarded and treated as a unit. Imaging optical sensor systems – such as laser scanners, stereo cameras and hyperspectral systems – or radar sensors produce important raw data that can be interpreted in relation to soil properties or plant characteristics. In this way, a field can be broken down into the quality of the individual plants: this already the object of research. The sensor data is merged with other data, such as soil or weather data. There are already practical solutions for accessing the various data sources, such as the universal, manufacturer-neutral data sharing platform for farmers, “agrirouter.“ The main challenges are interpreting the merged data and the resulting action instructions.
For example?
If the yield is lower in a particular part of the field, the question arises whether more or less fertilizer should be applied to that section to potentially increase the yield. For long-term action instructions, you need to have a wide range of knowledge about plants and soil and the interpreting of the latest sensor data.
When sensors are determining the soil conditions and how ripe plants are; when they are scanning the field and they know every plant; when, ultimately, robot machines are doing the work: Is the farmer on his tractor becoming an anachronism?
Definitely not. Just like if you use a washing machine, you don't sit at home for hours watching it. A farmer has plenty of important jobs if autonomous machines are working in the field. A high degree of automation helps make agriculture more sustainable. The processes and methods used in plant production and animal husbandry offer potential for ecological and economic improvements by incorporating farmers' knowledge and experience. One example is the design and development of a sensor to measure the moisture content of chopped corn. When the moisture content is 60 to 80 percent, identifying this value automatically is highly relevant from a business perspective. Technology alone does not solve any problems, but it is often a great way to help find a solution for them.
The tractor is, in the end, an auxiliary vehicle that mainly pulls other machines. Will it be retired if autonomous field robots take over?
A fascinating question. Because the tractor itself is actually a zero-purpose-machine. A tractor alone hardly helps anyone – except for the company that sells it, and perhaps the farmer, who can impress his neighbors with a large machine. Apart from that, the tractor is only actually worth anything when linked, mechanically and digitally, to an implement for agricultural processes. The implement is the important part of the unit, because it determines the process. Whether I am fertilizing, collecting hay with a loader wagon or working the soil, the tractor is a tool for a machine that does the actual work. This approach is called Tractor Implement Management (TIM). This means that smart implements for sowing, fertilizing or harvesting are networked with the tractor so that they become one unit. If, in the future, implements are to operate on their own as autonomous machines, i.e. the tractor function is integrated into the self-driving implement, then the good old tractor would actually be superfluous.
So soon it'll be So long, Tractor?
Not necessarily. The tractor is also a particularly flexible machine. It doesn't have a specific field of use. You can attach various machines and thus process modules, which makes the tractor a valuable tool. In principle, this makes it a flexible carrier platform for many different processes. We can't say right now where the tractor's path will take it. Autonomous tractors may have a role to play, and that is already being worked on.
In the BoniRob, you have developed a field robot that gets by without a tractor.
Our BoniRob represents one possibility for future work. We developed it together with Bosch and Amazone. The BoniRob is a flexible carrier platform that operates autonomously, without a driver. It has a very flexible design and different applications for different functions can be integrated in the middle. For cultivation, there is a module that investigates plant traits. Another module measures the condition of the soil. Another application can distinguish weeds from crop plants and control them mechanically using imaging sensors. It's like with the tractor: without an application – and by that, I mean smart hardware modules – the BoniRob has no function at all. But it's ideal for all sorts of applications when something is added to it. Then the farmer doesn't need to buy a different vehicle for every job.
With all due respect, just in terms of its appearance, the BoniRob is hardly beautiful. Agritechnica is traditionally a show for large agricultural machinery, giant tractors and powerful combine harvesters. Are we seeing the extinction of large agricultural machine dinosaurs when smaller, more flexible machines are increasingly being used?
I don't agree. In my eyes, even the little robots are gorgeous (laughs). It is true that current trends are being dominated by ever-larger XXL machines, but smaller autonomous systems in the XXS category are an alternative strategy for sustainable agriculture. When there are a few large machines, the failure of one system, for example a combine harvester, is a major cost factor. When there are many small systems, the economic risk is less. There is further potential in terms of ecological solutions. In the case of small, low-cost systems, the social issues around the world also vary, especially since over 90 percent of all farms worldwide are smaller than five hectares.
Availability is a key issue. For example, Continental is also developing tire sensors for agriculture that signal early on if a problem could arise with the air pressure. Will tires also take on a new meaning in Agriculture 4.0?
Of course. “Predictive maintenance” is a real keyword. I don't want to just see a problem when it's too late. Tires play an important role here. Currently, if a combine harvester breaks down due to a tire defect in the narrow harvesting window, it can have serious financial consequences for the farmer, not to mention the safety aspect. The fact that tires are integrated into the digital architecture is a positive development. For example, if in the future a tire sensor not only provides data on tire pressure, but also on slippage in the field, or on how wet the soil is, then important conclusions can be drawn. Supplemented by data from a weather app, a field robot might conclude that it would probably get stuck in the mud. This results in concrete instructions for the farmer. There is also potential in adjusting tire inflation pressures dynamically, from field to field. However, a tire sensor is only one of many components in precision farming technologies. For example, I see great potential in 3D technologies – including at Continental.
You raised the safety issue. How do self-driving machines make agriculture safer?
In a huge field in the North American breadbasket, there is, of course, no significant public traffic: it's all about efficiency. Nevertheless, the danger of accidents decreases the less people handle complex machines. And during other tasks, such as potato harvesting, there are lots of employees close to a harvesting machine. For example, as part of the “Agro-Safety” research project, we are testing the safety of autonomous feeding machines on farms. This is centered on sensors detecting people and switching the machine off immediately when there is any danger. The development of autonomous systems is – as in automotive sector – being accompanied by the introduction of hybrid systems, for example in the form of ADAS for autonomous driving and working. This so-called adaptive autonomy also includes autonomous and non-autonomous agricultural machinery working together on a field.